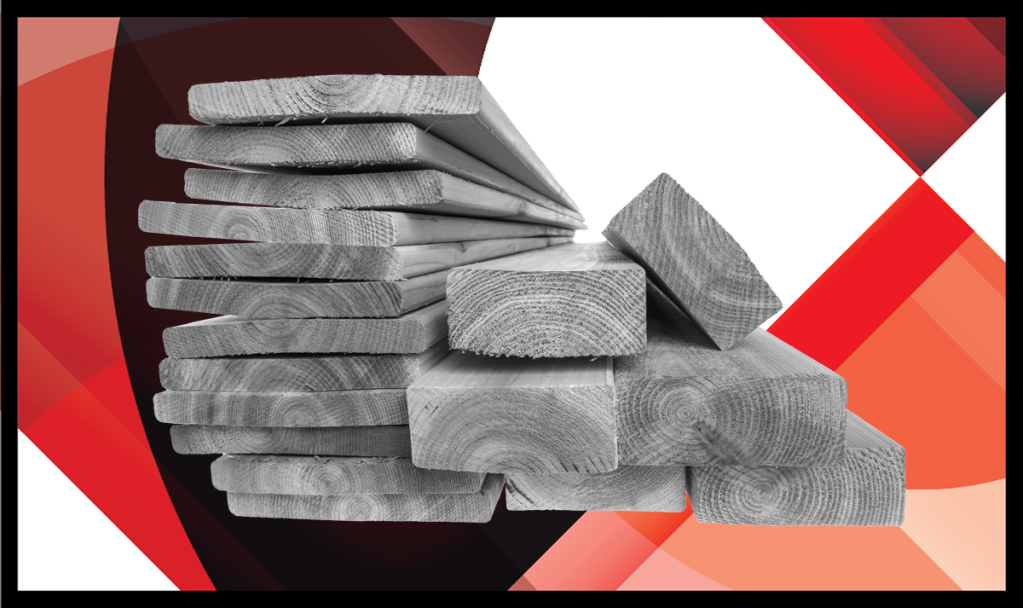
High lumber and appliance prices, as well as slow shipping and delivery times, continue to hamstring homebuilders in 2021.
It’s an issue that has been reported on at length by HousingWire, from the onset of the shortage to the crippling price increases — of both lumber and building materials — that coincided with the spread of the COVID-19 virus in the U.S.
Specifically, new home builders were hit extremely hard by the drop in inventory and, in part, by the subsequent skyrocketing prices, due to an increase in the number of homebuyers looking to take advantage of historically low mortgage rates.
“There is a disconnect between lumber supply and housing demand,” said Jerry Konter, NAHB vice chairman, in a statement from the NAHB. “U.S. sawmill output increased only 3.3% in 2020, and over the same period, single-family construction increased 12% to almost 1 million housing starts, and the remodeling market expanded 7%.
“We feel this mismatch between domestic production and rising demand for building materials is at the root of the unsustainable increases in lumber prices.”
Chuck Fowke, NAHB chairman, added that remodeling activity has also been held back by high lumber prices, and multifamily, affordable housing projects are also being delayed – or even shelved outright — due to the current complexity of financing.
“Lumber scarcity, and a dearth of building materials more generally, is absolutely still affecting everything,” he said. “And the increasing number of units authorized but not started — for example, the builder has pulled a permit but has not broken ground — is evidence of just that.”
As lumber prices went up, other suppliers — who were dealing with their own lack of product — began increasing their rates, as well. Before they knew it, builders were paying an inordinate amount of money for appliances and basic building materials, as well as lumber.
How did we get here?
Lumber mills in Canada began shutting down in the spring of 2020, when the virus began spreading throughout North America. Lumber inventory in the U.S. immediately began plummeting, but the demand for housing didn’t, since mortgage rates were at a sub-3% level.
As more and more people looked to take advantage of low interest rates, builders simply couldn’t keep up — there was a lack of materials, and the ones that were available had increased dramatically in price.
HousingWire reported back in March that lumber prices alone more than quadrupled since April 2020, to an astonishing $1,500 per thousand board feet. Today, lumber alone is adding nearly $36,000 to the final price of a new build.
This is on top of the dwindling lumber inventory the country has seen since the 1990s. Alicia Huey, NAHB second vice chair, recently said that the country was harvesting roughly 10 billion board feet of lumber per year in the 1990s. Today, she said, that number has fallen below 3 billion.
While new builds became increasingly more expensive for the eventual homeowner, existing homes all over the country were selling less than a week after they hit the market. And these new homeowners — many of whom were stuck at home due to company mandated work-from-home orders — couldn’t remodel, or replace the old appliances, or expand without paying a king’s ransom for supplies.
Suppliers, appliances still in short supply
It’s not completely fair to blame lumber mills for every supply delay, price increase, and skeleton workforce in 2020 and 2021, noted David Logan, NAHB senior economist and director of tax and trade policy analysis. You can, however, blame the pandemic — the genesis of the housing crisis, Logan said — and, strangely, some ill-timed weather.
“The success of shipping and supply chains have been so regionally dependent during the pandemic,” Logan said. “The popular complaint is that all suppliers are moving slowly, and they are — but some companies are only delivering in the region they service out of. They’re trying to cut down on risk by not shipping all over the country.”
The butterfly effect from supply and shipping companies only working in a smaller, centralized area is then easy to trace: A builder in Maryland who usually orders appliances from a company in Texas might have to pivot to ordering from a more expensive outfit on the east coast. While travel time might be cut in half, the east coast company knows demand for its product is higher and raises its prices.
“We obviously do a lot of overseas shipping and importing that you would expect to take a hit [with the pandemic], but even our domestic supply chains have really suffered,” Logan said.
Specifically, the cost — and scarcity — of new appliances for homes has been an added thorn in the side of homebuilders and prospective buyers, as the median price of refrigerators, washing machines, and ovens had increased 10% by the end of 2020, Logan said. Those prices have stabilized as the calendar turns to June 2021, but delivery time is still a problem, he said.
“We’re talking up to six months for delivery of appliances in some cases,” Logan said. “And that’s another regional issue. The country gets a lot of refrigerators and refrigerator parts from Mexico, for example, and they were in a lockdown for a long time. That really hurt anyone ordering freezers or refrigerators.”
Then, just as prices improved for the first time in months, a once-in-a-lifetime winter storm hit Texas in early 2021, further disrupting supply — and builder schedules — throughout the country.
“There are a few major companies in Texas, for example, that are major suppliers of refrigerator insulation and other appliance accessories, and those were completely shut down for a few days in February,” Logan said.
Thus continues the immensely frustrating cycle builders are in: The pandemic shut down lumber mills, which drove up the price of lumber, which in turn drove up the prices of everything needed to build a home, Logan said.
“What we’ve seen over the past year, in terms of building supplies, appliances and other materials, is either prices have increased dramatically, or the items are in short supply,” he said. “And from the most basic, Economics 101-perspective, that doesn’t make any sense.”
Vaccines are critical for a return to normalcy
The continued distribution of the multiple COVID-19 vaccines is key to a return of affordable prices and shorter delivery times, according to multiple experts interviewed for this story. Lumber mills returning to full strength will certainly help, but those still operating at less than 100% capacity are doing so, in part, to keep workers healthy.
“Really, it’s going to take the working share of the population getting vaccinated and back to work for things to really improve,” Logan said.
Builders have told HousingWire before that they struggle to find full crews to build homes, as enhanced unemployment benefits — enacted by the government to combat the effects of the pandemic — are keeping workers at home. And even if they aren’t receiving a large unemployment payment, the risk of getting sick isn’t worth it, they said.
Fowke said a return to normalcy sometime in 2022 — when more of the U.S., and the world, is vaccinated — is more realistic.
“Policymakers need to act,” he said. “We’re not going to return to anything normal [before 2022] given the strong housing demand, and strained bottlenecks.”
@Tim Glaze, Chuck Fowke references “the increasing number of units authorized but not started — for example, the builder has pulled a permit but has not broken ground…”
Do you know if NAHB tracks this, or if there is a time-series chart of authorized but not started available through Corelogic or others?