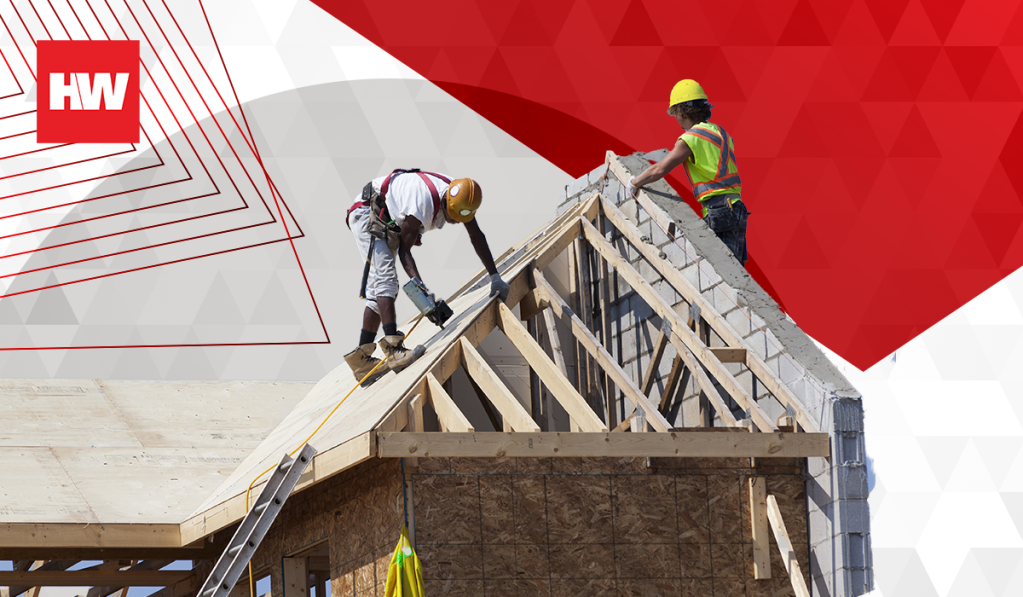
Nate Noel’s problem isn’t a lack of work. It’s everything else.
“I used to be able to get guys no problem, but now I am bidding on guys and having to raise pay in order to keep the guys I already have, which is just continually raising my costs,” said Noel, the president of HNN Builders, a custom homebuilder in the Chicago area. “I was working with a subcontractor on a project and the initial bid was $35,000 and the guy came back at $50,000 for the work because one of their guys left to start his own company and was trying to steal all their employees. So, they went from having to pay their guys $22 an hour to paying $30 an hour just to stay around.”
Then there are the global supply chain issues, which have frustrated small-time homebuilders like Noel and the heads of publicly traded builders alike.
“Every day is a roller coaster clause,” Noel said. “Lumber is of course a big one that people across the country saw, but we are seeing it everywhere from your spray foam insulation to your windows. Windows have gone up probably about 20% and usually they would be four to six weeks, but now it’s 12 to 14 weeks. So we are working on projects and when we got the quotes it was one cost and price, but when we go to order after getting the plans and permits finalized the price has gone up and now you’re like ‘I didn’t plan on three extra months to have to wait for windows.’ Luckily we did a lot of framing when lumber prices were about $3 for a four by eight, but last week it was about $9.”
Owing to a historic inventory crunch, new construction is playing a more prominent role in the housing inventory landscape in decades.
In December 2021, 34.1% of U.S. single family homes on the market were new builds, according to a report by Redfin. A year prior, only 25.4% of homes for sale were new construction.
Currently, over 1.7 million homes are under construction, the highest level in decades. But homebuilders big and small continue to run into the same problems – building permits are on file, contracts with buyers are inked, but subcontractors often don’t show, and access to materials have led to longer build times and cost overruns.
To boot, many homeowners are choosing to remodel their current home instead of buying a new one, making it even harder to get skilled labor and the materials they need.
The National Association of Homebuilders/Royal Building Products Remodeling Index (RMI) finished 2021 with a strong reading of 83. During the first quarter of 2020 the index had a reading of 48.
“We have been in a perpetually bare market for inventory for so long now that builders are having to fill the demand and I am not sure when it is going to end, which is crazy,” said Noel.
The forest from the trusses
In May of 2021, lumber prices soared to over $1,500 per thousand board feet of random lengths framing lumber. While prices declined throughout the spring and summer, dipping to under $400 in early September, they quickly rose again, coming in above $1,200 in mid-January 2022. Due to the volatility of commodity and labor prices, Noel instructs his clients to build a bigger “cushion” into their budget than they normally would.
“The biggest lumber producers – and the lumber industry at large – has not really adjusted output over the past year and a half compared to what output was prior to the pandemic,” said David Logan, the director of the NAHB. “It is no secret that housing demand has been on a tear, rising higher and higher for a myriad of reasons, yet output in the sawmill industry has remained relatively flat, which is obviously contributing to higher prices. So, we have a fairly constant supply, but there is just unrelenting demand.”
Like other sectors, the mill industry and the construction industry have been hit by labor shortages throughout the past two years. Although residential building construction employment is up 5.3% compared to its pre-COVID level, the NAHB estimates that the residential construction sector would need to add 740,000 workers a year just to keep pace with the industry’s growth, retirements and departures.
There is some good news from the sawmill industry, which plays a pivotal role in the homebuilding ecosystem, as employment is back to the level it was pre-pandemic, in January 2020.
“This is good news for the mill industry, but employment in that industry has been declining since the beginning of 2017, which coincidentally is when tariffs on Canadian lumber went into place,” Logan said.
Tariffs on lumber imports from Canada were put in place in 2017 at the urging of the U.S. Lumber Coalition, which felt that U.S. lumber producers were being harmed by the amount of Canadian lumber being exported to the U.S. As of right now lumber tariffs are at 17.9%, but in late January the Commerce Department issued an administrative review to reduce the tariff to 11.64%. Homebuilders should not get too excited, however, as this is the third administrative review called on this issue, but the NAHB remains optimistic. The trade group is supportive of the Biden administration’s move to reduce duties from 17.99% to 11.64% on softwood lumber shipments coming in from Canada.
But rising lumber prices and limited supply is just part of the homebuilding industry’s problem. According to Ali Wolf an economist at Zonda, nearly everything needed in the homebuilding process is facing some sort of delay and subsequent price increase.
Prices for gypsum, a key component for drywall, rose 21% in 2021 according to the Producer Price Index from the U.S. Bureau of Labor Statistics and no new gypsum production is expected to come on board during 2022. Production of roofing materials is also not expected to increase this year. Window suppliers are receiving partial orders from component suppliers like glass, hardware and extrusions, which is further slowing down production. It’s been so hard to find garage doors that the New York Times wrote a feature about the magnitude of the problem.
Siding supply is expected to remain tight throughout the year, but siding manufacturer James Hardie announced plans to open additional lines and plants later this year and in early 2023.
“A lot of these things are byproducts of softwood lumber,” Logan said. “With your windows, doors and millwork, that value added process, after those companies had to pay exorbitant prices for the raw material, they then have to wait for a long time for their product because the production is lagged.”
Disruptions and shovels
With the supply of these necessary goods backlogged, it is no surprise that homebuilders across the country, both big and small, are having trouble getting their hands on building materials. Despite witnessing revenue soar 26% year over year in 2021 to $13.9 billion, Pulte Group executives remain subdued in their expectations for 2022.
During its 2021 fourth quarter earnings call, Ryan Marshall the president and CEO of Pulte Group, the country’s third most prolific home builder, repeatedly bemoaned the “labor shortages” and “significant disruptions in the supply chain” that the industry is facing.
“The supply side of the equation has been extremely challenging, with no clear signs as to when things will get better,” Marshall said during the earnings call.
Commenting on Pulte’s fourth quarter earnings, BTIG homebuilding analyst Carl Reichardt said: “PHM has a scale advantage over many smaller peers, which will help the company manage ongoing supply chain disruptions that appear likely to persist.”
Lennar, the country’s second largest homebuilder, also bemoaned the supply chain bottlenecks during their September earnings call, despite building and selling more homes than they did in 2020.
“The largest players in the industry obviously have a ton of buying power that your typical homebuilder just doesn’t have,” Logan said. “When the high production builders are put on allocation. Which they have been at points since the start of the pandemic, you know that it’s 10 times as bad for your typical builder who is building just five to 10 homes a year.”
Even with these challenges, homebuilder confidence in the market for newly built single-family homes was still relatively strong in January, with a National Association of Home Builders (NAHB) and Wells Fargo Housing Market Index (HMI) reading of 83. Since November, homebuilder sentiment has hovered around the 83 to 84 level, roughly the same rate as it was in the spring of 2021.
Housing starts are also looking up, rising 1.4% month over month in December to a seasonally adjusted annual rate of 1.70 million according to a report by the U.S. Department of Housing and Urban Development and the U.S. Census Bureau, reaching their highest level in the past nine months.
“Housing demand has outstripped supply since 2009,” First American deputy chief economist Odeta Kushi said in a statement. “The last housing starts report of 2021 is a positive step towards bridging the gap between supply and demand, as an estimated 1,337,800 housing units were completed in 2021 – 4.0% above the 2020 figure. 2021 was a strong year for construction.”
In addition, the number of building permits issued in December rose 9.1% from November, but that does not necessarily mean that homebuilders will have the supplies and the labor to keep up with this demand.
“The shortage of skilled labor, materials and lots, are headwinds to increasing the pace of new construction,” Kushi said. “The good news in the December housing starts report is the number of single-family homes permitted, but not started declined to its lowest level since April 2021, but remains elevated compared to pre-pandemic.”
But Noel says that from his vantage in Chicago, keeping up with the demand for new homes is going to remain a challenge in 2022, and likely beyond.
“We are still seeing about a four million house deficit across the U.S. in new construction and homebuilders have not really started making up for it because of the risk,” he said. “Unless builders are putting up entire suburban sprawl type neighborhoods, they just don’t have the margins right now. I just don’t see prices of lumber and everything coming down and helping builders increase their margins, so a lot of builders are sitting on the sidelines or just doing custom stuff. I know a ton of builders in Chicago that just decided to get out of it in the last two or three years just because it’s never fun to continually having to give bad news to their clients.”